Needle Loom Machine
A shuttle needle loom machine is a commonly used weaving equipment, its working principle is relatively simple, that is, the computer control system quickly moves various threads through the fabric up and down the process, so as to complete the process of weaving. There are many classifications of looms, according to the weft insertion method of weaving, which can be divided into shuttle looms and shuttle needle loom machines. The weft insertion machine with a shuttle loom is a loom that uses traditional wooden shuttles or plastic shuttles for weft initiation. Due to the large volume and heavy weight of the shuttle, the shuttle is repeatedly projected back and forth, so the machine has high vibration, high noise, high energy consumption, slow speed, and low efficiency. The weft insertion methods of shuttleless loom looms are also varied, including rapier rods, air jets, water jets, sheet shuttles, and multi-shuttle (multi-phase).
The Development History Of Shuttleless Needle Loom Machine
- In 1949, Czechoslovakia first made an air jet loom. Due to the lack of control measures for the diffusion of airflow, the width of the woven fabric was only 45cm.
- In 1956, the development of combined pipe segments to limit the spread of airflow led to a breakthrough in jet technology.
- In 1963, the Netherlands developed auxiliary nozzle weft insertion technology, which greatly increased the width and speed of the loom.
- In the 1970s, a new form of restricting airflow diffusion – special-shaped buttons came out, which made new progress in the range and quality of fabrics woven by air-jet looms.
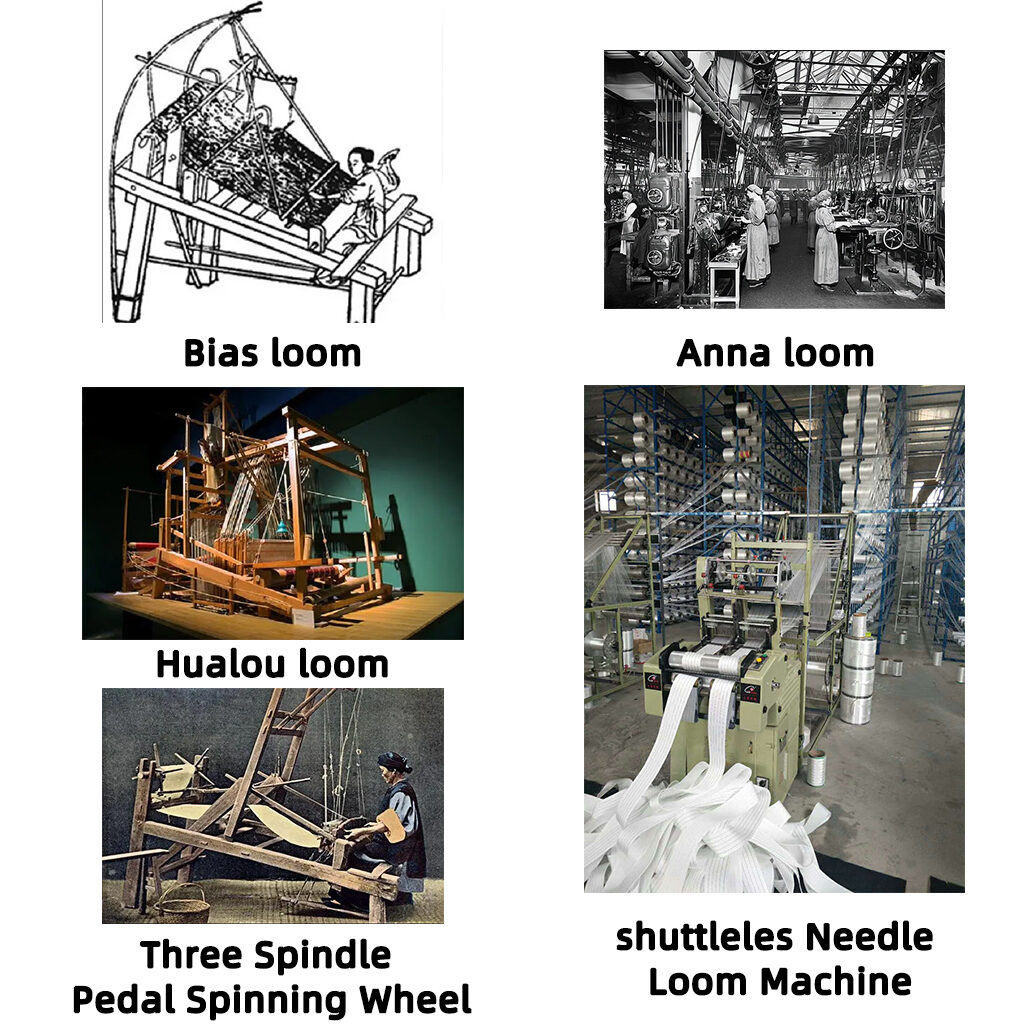
Weft Insertion Principle
Jet weft insertion is the use of air as the weft insertion medium, with the ejected compressed air flow to produce frictional traction on the weft yarn traction, the weft yarn is brought through the shuttle, and the jet generated by the jet is used to achieve the purpose of weft insertion. The characteristics of air-jet weft insertion: the characteristics of air-jet weft insertion are high speed, high tension, and small shed, and the requirements for raw yarn and semi-finished products are relatively high. Among several kinds of shuttleless needle loom machines, the air-jet loom is one of the highest speed, due to reasonable weft insertion mode, high weft rate, simple and safe operation, wide adaptability, less material consumption, high efficiency, high speed, low noise, and other advantages, has become one of the most promising new cloth machines. Since air-jet looms use the air-weft method, the biggest disadvantage is the higher energy consumption. Jet insertion is a passive method of weft insertion in which the weft yarn has little tension and no control when flying over the shuttle, so there is a lack of sufficient traction for the weft yarn with high linear density or fancy yarn. At the same time, the opening state of the warp wire has a great influence on the quality of weft insertion, and it is easy to produce fabric defects such as weft shrinkage and weft foldback.
Working Principle Of Shuttleles Needle Loom Machine
The shuttle needle loom machine is mainly composed of five major mechanisms: opening mechanism, weft feeding mechanism, locking mechanism, weft beating mechanism, and winding mechanism.
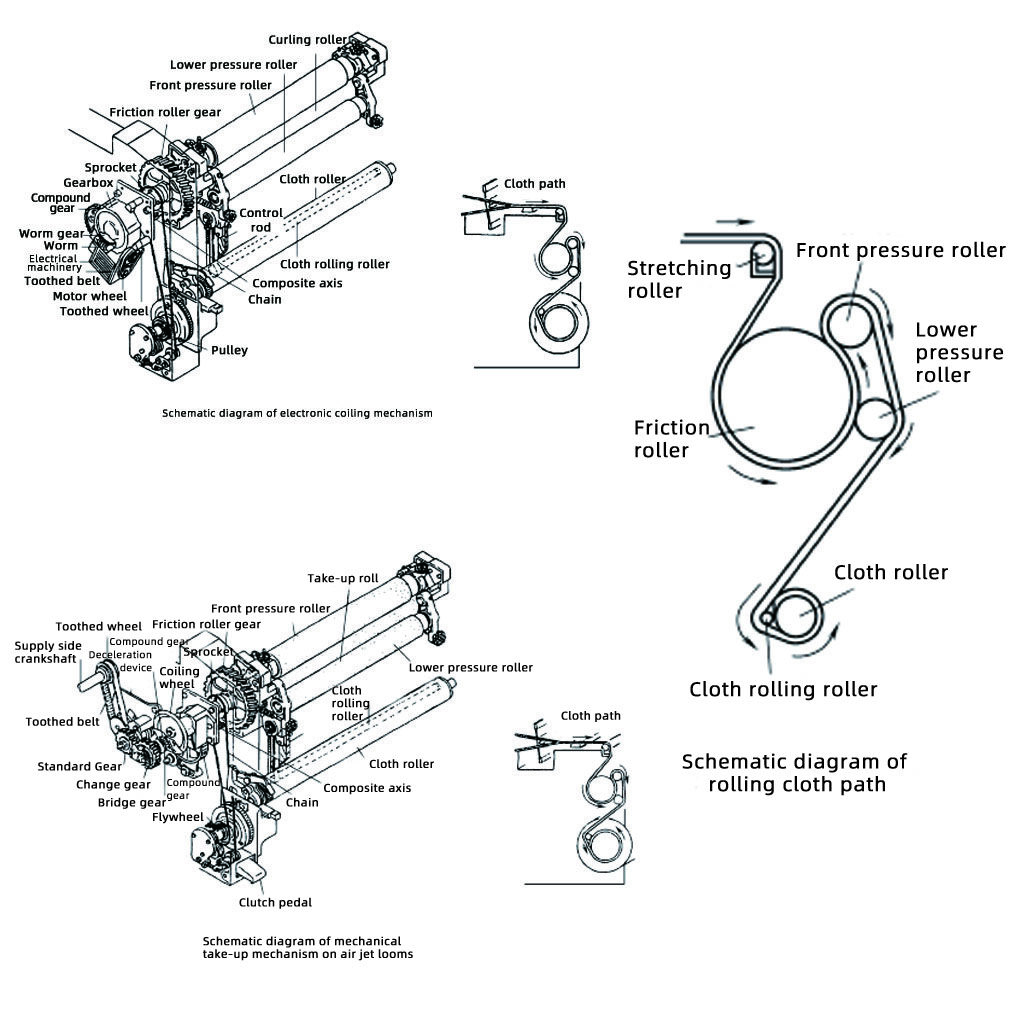
- Mouth mechanism: In order to interweave the warp yarn and the weft yarn into a textile on the loom, it is necessary to first divide the warp yarn into two layers, create a shuttle, and then introduce the weft yarn. Therefore, the warp yarns need to be threaded into the head’s eyes according to certain rules. When the heddles move up and down along with the head frame, the warp yarns will separate up and down along with the adjustment of the head frame, creating an opening for the weft yarn to penetrate. According to the organizational needs of the fabric, multiple heald frame design openings can be adopted (2 heald frames for weaving plain fabric).
- Weft feeding mechanism: Weft feeding should be used to introduce the weft yarn into the shuttle so that the weft yarn and the warp yarn are interwoven into a glass fiber belt. The weft feeding mechanism of the high-speed shuttleless needle loom machine has 3 characteristics: (1)Faster weft feeding speed; (2)The amount of weft yarn rolled up is large, the time for changing the weft yarn is small, and the operation rate of the loom is large; (3)Weft sending is double weft/time. Due to the fast weft feeding speed, the weft prevents the weft yarn from being broken due to excessive tension. It is necessary to adopt a positive weft-feeding installation to reduce the tension of the weft yarn and ensure normal weaving.
- Overlock mechanism: The fabric structure of the double weft is caused by a weft feeding needle, and there are two main ways to lock the seam: (1)Hook the weft with a seaming pin, not the seam. This organizational structure, such as when there are few weft yarns, the weft yarns will be loose and prone to loose banding. (2)Lock the edge with the lock line, generally use the warp lock edge, hook the lock edge line with a hook needle, form a coil, lock the weft yarn; Its basic action is that the crochet needle first hooks the lock line, and then reciprocates, forming a coil in the hook line and then de-looping, so as to form a continuous edge line and lock the weft line.
- Beating mechanism: The weft yarn introduced into the shed is guided to the weaving fell and interlaced with the warp yarn by means of the beating mechanism to form a textile. The width of the fabric and the relative density of the warp yarns are determined by the reed in the beating-up mechanism. The ordering of the weft yarns in the textile and the buckling of the warp and weft yarns are determined by the different tensions and deformations of the warp and weft yarns during beating-up.
- Coiler: The take-up mechanism is a device that pushes the warp yarns to shift and pulls the woven tape away from the fabric fell. In order to improve the actual efficiency of the take-up, the main role of the take-up roller is generally a rubber roller. After the glass fiber tape comes out of the take-up roller, it is now Generally, there two ways to take the belt: (1)The unwound glass fiber tape falls into the tape storage box first and then is divided into coils according to a certain length on the decompiler. (2)The glass fiber tape is directly rolled into a roll, and the roll is directly formed during the ribbon weaving process, which can reduce the splitting process. Before the shuttleless needle loom machine starts working, all kinds of thread ends need to be threaded and arranged, and then the electronic control system controls the movement of the needle bar, and the thread ends move up and down through the fabric from various positions to complete the whole weaving process. The weaving speed of the shuttle needle loom machine is very fast and can reach thousands of weaving times per minute, which greatly improves production efficiency.
Components Of A Shuttleles Needle Loom Machine
- Support frame: The support frame is one of the important parts of the ribbon loom. It is generally made of steel materials. Xuzhou Qixing Machinery Co., Ltd. can bear the full weight of the machine and keep the balance and stability of the machine.
- Extense: This assembly is used to control the weaving tension of the machine and usually consists of a series of tension wheels and pull wires. By adjusting the tension of the tension frame, the flatness of the webbing can be higher, thereby improving the quality of the webbing.
- Weaving system: it is the core system of the ribbon loom, including the active power and transmission system of the ribbon loom, and is the key to realizing ribbon production. The weaving system generally includes key components such as a winch, weft machine, needle bar, and bottom plate.
- Electronic controller: This component is used to control the functions of the loom, such as the rotation speed of the motor, the adjustment of the webbing tension, etc. Controllers often have multiple control modes that can be adjusted according to different production requirements.
- Motor: The motor is the main power source of the loom, usually using a DC motor or AC motor. The speed and power of the machine usually depend on the number of poles and power parameters of the motor.
- Transmission system: The transmission system of the loom is an important piece of equipment for connecting the spindle and the weaving shaft, usually including transmission parts such as belts, wheelsets, and gears.
The above are the main components of the ribbon loom, and there may be other components and auxiliary components for different types of ribbon looms. It should be noted that the number and form of components of each ribbon mechanism may vary to meet the needs of different types of ribbons and different motor powers.
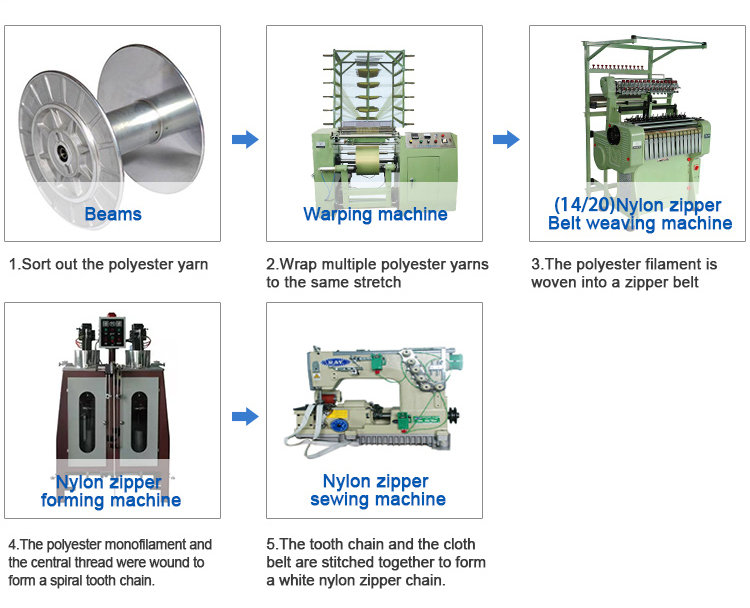
Scope Of Application And Fabric Types
Early air-jet looms had a small range of adaptation, mainly to produce white-grey fabric, and the cloth width was small, the speed was slow, the fabric was limited, and the fabric quality was not high. However, since the early 80s of the 20th century, with the development of air-jet loom special-shaped reed and relay weft insertion technology and the application of electronic computers, sensors, and frequency conversion speed regulation technology, the speed of air-jet looms and the automatic monitoring level of looms have been greatly improved, especially the rapid development of air-jet looms in the past 10 years, which has made air-jet looms have many advantages such as high quality, high speed, high output, and high automatic control level, and the range of variety adaptation has been greatly improved. The width of air-jet looms has increased from 190cm and 280cm to more than 340cm, 360cm, and 400cm; The main nozzle has been increased to the double nozzle and four nozzles; Multi-color weft insertion system controlled by computer software for 4 to 12 color weft selection; The raw materials of weft yarn can be chemical fiber filament, chemical fiber staple fiber, cotton yarn, wool yarn, glass fiber yarn, various fancy yarns, etc.; Available in a wide range of high-end fabrics ranging from high-end, high-end fabrics to coarse-count high-density fabrics, DORNIER air-jet weaving machines have been used to produce technical fabrics such as filter fabrics, emery twill fabrics, steamed fabrics, and fiberglass wallcoverings. The new air-jet looms of Bijano in Belgium and Tsudakoma in Japan are also equipped with electronic jacquard, dobby, and other shedding systems to adapt to the production of various fabrics.
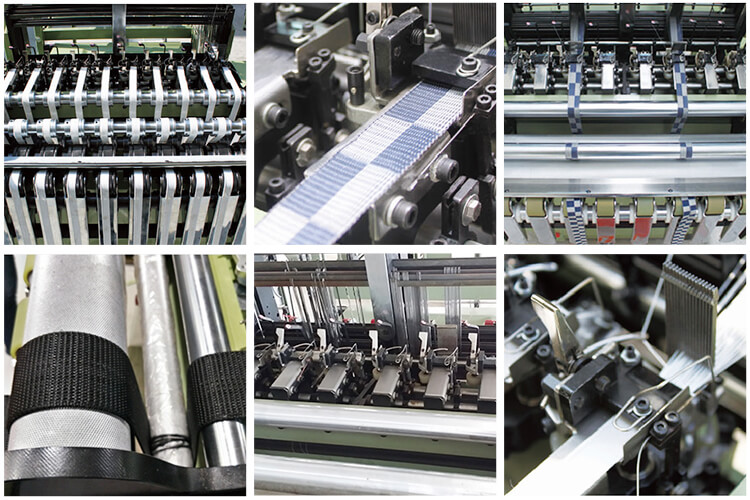
Classification Of Shuttleless Needle Loom Machines
The classification of shuttleless needle loom machines can be classified according to the number of heads of the machine and the scope of the machine preparation; According to the number of heads, it can be divided into 2 heads, 4 heads, 6 heads, 8 heads, 10 heads, 12 heads… The scope of preparation can be divided into 16mm、25mm、30mm、35mm、40mm、45mm、55mm、65mm、80mm、110mm、165mm、200mm、300mm… All specifications can be customized according to customer needs to match the products produced by customers.
According to the number of heads: the main factor of the shuttleless needle loom machine according to the number of heads is to customize the number of heads of the machine according to the customer’s output needs, the higher the output required by the customer, the more heads are required, the corresponding machine price is more expensive, the larger the machine footprint, so the machine is not the more heads, the better, according to its own capacity to choose the right machine is very necessary.
According to the preparation range: the preparation range is determined according to the width of the product to be knitted, if you need to weave a wide width of the product need to use a wider machine, our company’s design will recommend the most appropriate machine according to the product compiled by the customer.
Shuttleles Needle Loom Braiding Material
There are many kinds of raw materials suitable for shuttleless needle loom machines, such as nylon (nylon PA), polypropylene (PP), polyester (PET), aramid, high-strength polyethylene, cotton thread, glass fiber, carbon fiber, silicon carbide fiber, basalt fiber, etc. The weaving of composite materials. Different materials are suitable for different industry applications, and the configuration and accessories of the shuttle needle loom should be changed according to different materials.
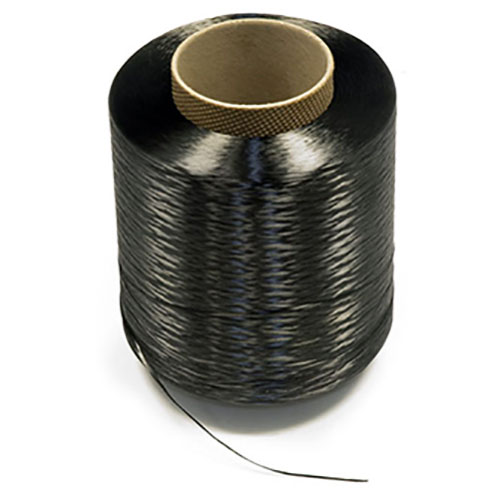
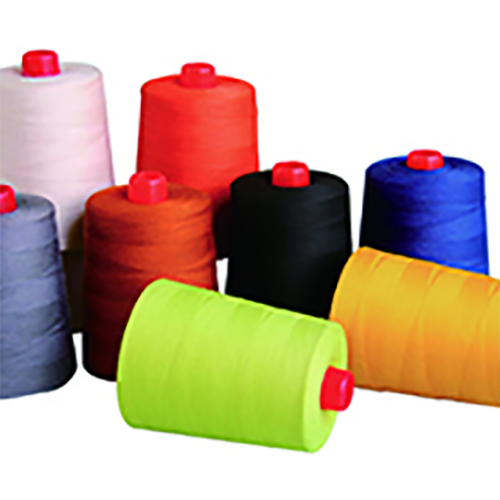
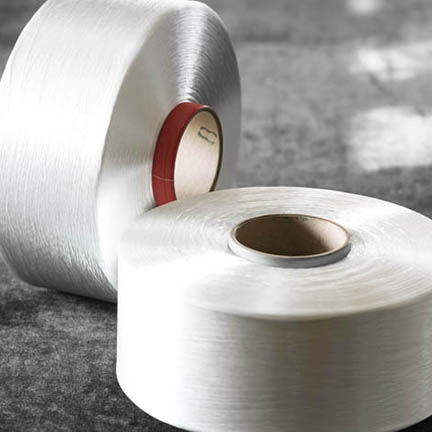
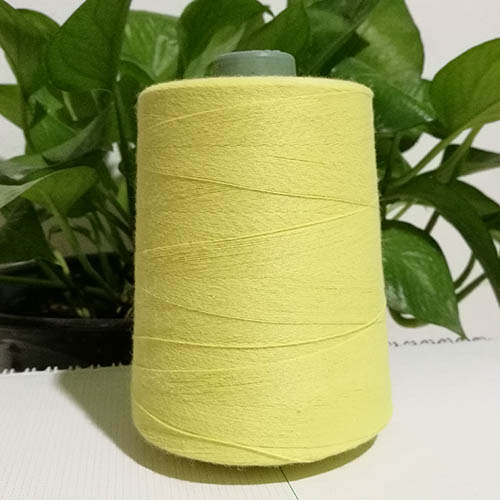
Carbon Fiber
Polyester
Nylon
Yoshin
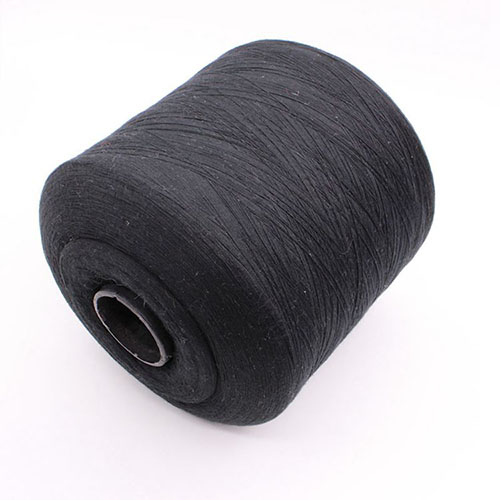
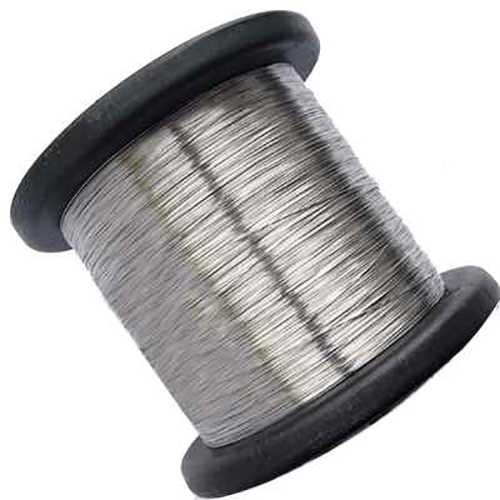
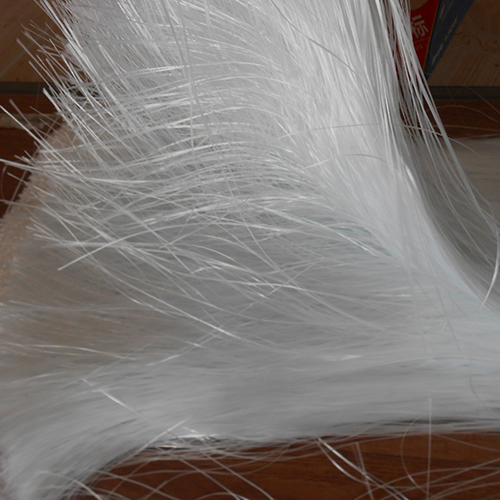
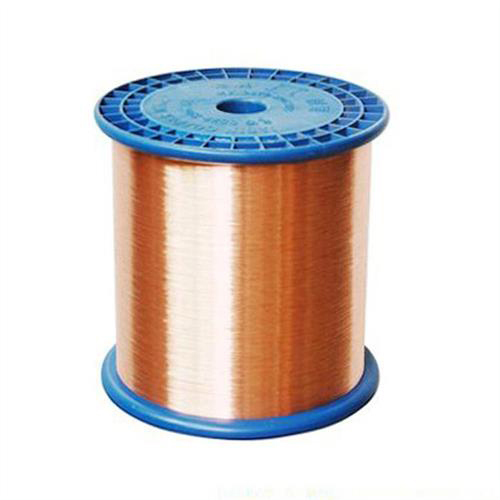
Polyester
Stainless Steel Wire
Glass Fiber
Copper Wire
Shuttleles Needle Loom Application Industry
The shuttle needle loom machine is suitable for weaving non-elastic or elastic webbing, such as underwear belts, ribbons, shoelaces, safety belts, sling belts, PP belts, etc. The products are widely used in clothing, bags, shoes and hats, automobiles, and other industries.
Clothing industry: clothing accessories, clothing materials, shoe materials, shoe laces, belts, headwear, hat ropes, elastic bands, wavy belts, underwear belts…
Luggage industry: luggage straps, backpack straps, handbags…
Automotive industry: seat belts, trailer belts…
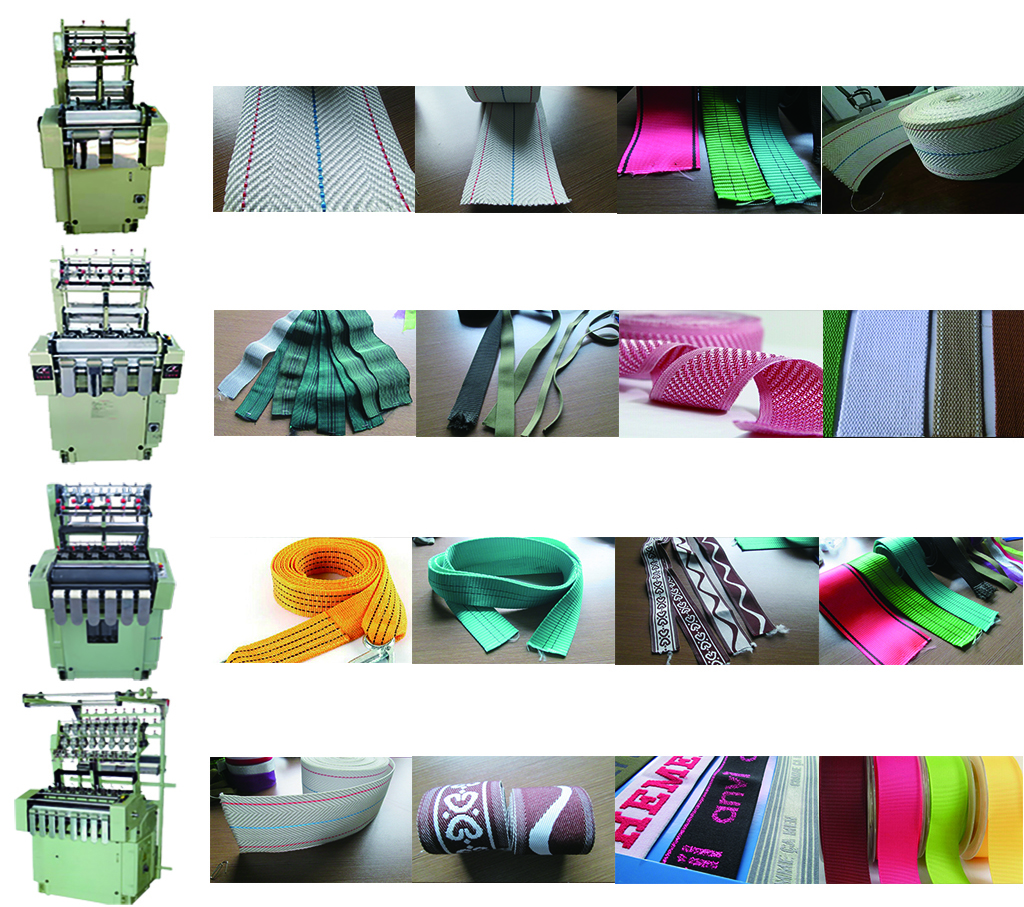
Comparison Of Air Jet Loom And Other Shuttleles Needle Looms
- Rapier loom: Rapier looms have unique advantages in variety adaptability, but the weft insertion rate is lower than air-jet looms, only 1400m/min, about 50% of air-jet looms; The yarn return rate is higher than other shuttle needle looms. At present, rapier looms are mainly used for the production of small-batch and various weft yarn fabrics such as decorations.
- projectile loom: The sheet shuttle loom has advantages in weaving extra-wide fabrics and high-grade decorative fabrics, but the weft entry is lower than that of the air-jet loom, which is 1200m/min; The energy consumption used for the acceleration of the shuttle only accounts for 15%, and the energy consumption is unreasonable; High requirements for the material performance and weaving accuracy of the torsion shaft of the spindle; It is expensive and has a large one-time investment cost.
- Water jet loom: The waterjet loom has limitations in the quality of weaving and is only suitable for the weaving of hydrophobic yarns such as synthetic fibers and glass fibers. The relevant components on the loom should be made of stainless steel materials.
- multiphase loom: Multiphase weaving machines can be woven with extremely high weft rates. However, it can only produce simple ordinary fabrics, and the electricity consumption per square meter of fabric is higher than that of other shuttle needle looms.
Company Profile
Our predecessor is Xuzhou Hongqi Machinery Factory, which was established in 1971 and changed to Xuzhou Qixing Machinery Co., Ltd. in 2001.
The shuttleless needle loom machine is our main product, and many universities and laboratories cooperate, products are all independently developed and produced, and have 30-degree patents. Our shuttleless needle loom machine has CE and ISO certification, can adapt to the voltage needs of different customers in different countries, and has been exported to more than 40 countries. We can provide complete solutions, including packaging, loading, payment, sea freight, customs clearance, and more.
We can customize the configuration, shape, size, color, etc. of the shuttleless needle loom machine according to your needs, or OEM your brand, support you to sell and market in your country. You are welcome to consult at any time, and we will reply to your email within 24 hours.